“The aerospace industry has the most demanding clients imaginable. They require materials that can withstand the most extreme conditions. Entering the Earth’s atmosphere at a speed of 25,000 kilometers per hour takes its toll on the structure and integrity of the spacecraft. Only the highest quality of materials will suffice,” says Luc Dionne, CEO of Tekna.
Which is why the aerospace industry flocks around Tekna, a world-leading – or perhaps an out-of-this-world-leading – supplier of advanced materials solutions. With its patented plasma technology, Tekna produces high quality materials which are used to 3D print vital parts of spacecrafts.
Advanced materials from Tekna are supporting advances in the aerospace industry. Spacecrafts and satellites are launched or doing orbits around the Earth with Tekna powders integrated into smaller or larger parts of the structure.
“Between 50 and 100 satellites in space have parts produced with Tekna powder,” estimates Dionne.
He cannot disclose which parts are made from Tekna powders, but he can reveal that they are made with the highest quality of titanium and aluminum powders.

INCREASING VOLUMES
Volumes are increasing. Tekna deliveries grow by approximately 30 per cent year-over-year. Today, the Tekna production facility in Canada has an annual capacity of nearly 300 tons of titanium and aluminum powder of various sizes, and the company keeps on increasing the factory output every year. A second factory is located in Mâcon, France.
Offering high strength-to-weight ratio, 3D printing of parts has proven especially suitable for the aviation and aerospace industries. If a part is designed for 3D printing, its weight can be reduced by up to 75 percent, while its strength remains the same.
Aerospace requirements are extreme. Tekna powders undergo a rigorous test regime to qualify for the industry. Among Tekna clients are suppliers to both national and private aerospace programs.

HYPERSONIC FLIGHT RESEARCH
Also for the aerospace industry, Tekna has developed another product based on its plasma technology; a PlasmaSonic wind tunnel used for hypersonic flight research.
Tekna PlasmaSonic products are high enthalpy ground testing facilities used in experimental investigations of spacecraft heat shield materials and thermal protection systems. The main purpose of this equipment is to reproduce the severe conditions encountered by an object when travelling at high velocity or during its re-entry into the Earth’s atmosphere.
Tekna’s PlasmaSonic solutions are key to advancing the development of new thermal protection materials required for hypersonic flight and orbital re-entry vehicles.
So far, Tekna has produced and sold five PlasmaSonic systems. Clients are typically research institutions, such as the University of Illinois in Chicago, which has purchased a system. Tekna is also about to deliver a PlasmaSonic system to a non-disclosed high-profiled private aerospace company.
Tekna regularly supports the largest research laboratories and original equipment manufacturers worldwide to accelerate materials development and push the limits of hypersonic flights for aerospace and defense applications. The company has identified a potential CAD 220 million market of similar plasma wind tunnel material testing facilities.
Tekna’s PlasmaSonic portfolio includes an array of automated plasma wind tunnels, with built-in instrumentation and robotics that are designed to replicate for hours high altitude (around 70 km) and high velocity (up to Mach 25) faced by a spacecraft during its re-entry into the atmosphere.
“There are so-called thermal protective shields around these vessels which are supposed to protect the various parts when they hit the Earth's atmosphere. Historically, it was rare to reuse large parts of these vessels. With our wind tunnels, however, it is possible to test the materials so that you can optimize and find materials and parts that can be reused. Then both the costs and the environmental footprint can be reduced significantly,” explains Dionne.
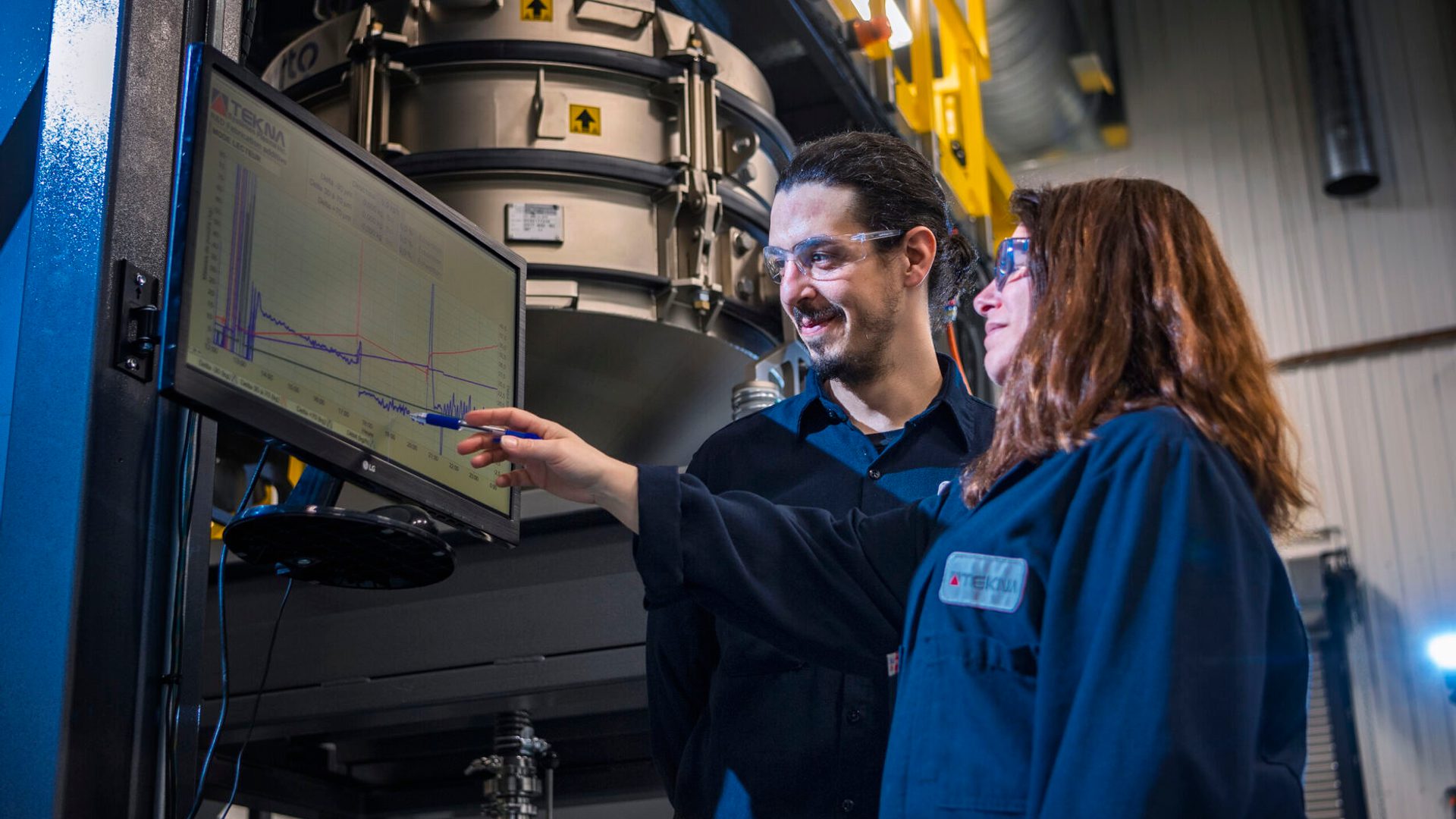
10 YEARS WITH ARENDALS FOSSEKOMPANI
In 2014, Arendals Fossekompani became the largest owner of Tekna. In 2021, Tekna went public and was listed on Euronext Growth and later relisted on the Oslo Stock Exchange main list.
“Tekna demonstrates the ability to provide cutting-edge technology to some of the most demanding customers in the world. Its client base is impressive. We are excited to be part of the journey,” says Benjamin Golding, CEO of Arendals Fossekompani.