Tekna is a world-leading supplier of advanced materials solutions. With its patented plasma technology, the company produces high quality metal powders used to 3D printed parts vital to the aeronautic, aerospace, energy, and cutting-edge industries such as Formula 1.
And perhaps most precious for humans, within the world of medical applications.
From powder to prostheses
Arendals Fossekompani- an active owner and support of Tekna (OSE: TEKNA) sat down with Christophe Tisserand, Tekna Sales Director in Europe for Powders to gain a better understanding of how a spherical powder can be transformed into a customized prothesis.
Tisserand studied Mechanics and Automation and brings with him a decades-long background working with machine and parts supply sales for the companies Renishaw, VOLUM-e, and Spartacus3D. He joined Tekna in the middle of 2023 and has been helping the company continue as a leading supplier of their Ti64 game-changing material.
“What’s fascinating is that this powder quickly became a key product for manufacturers of medical and dental applications,” says Tisserand.
Breaking down Ti64 (Titanium Alloy Ti-6Al-4V)
The official name for Tekna’s powder is Ti-6Al-4V titanium alloy powder. Primarily produced in Quebec, Canada, it has a high level of sphericity, low oxygen content, high density (bulk and tapped) as well as controlled grain size. These properties are necessary to make it compatible with even the most demanding industrial applications.
“By leveraging its proprietary plasma atomization technology, Tekna produces Ti64 powders that are highly spherical and free from internal porosity. This results in powders with higher density and flowability, which translates into superior mechanical properties in the final printed parts,” explains Tisserand.
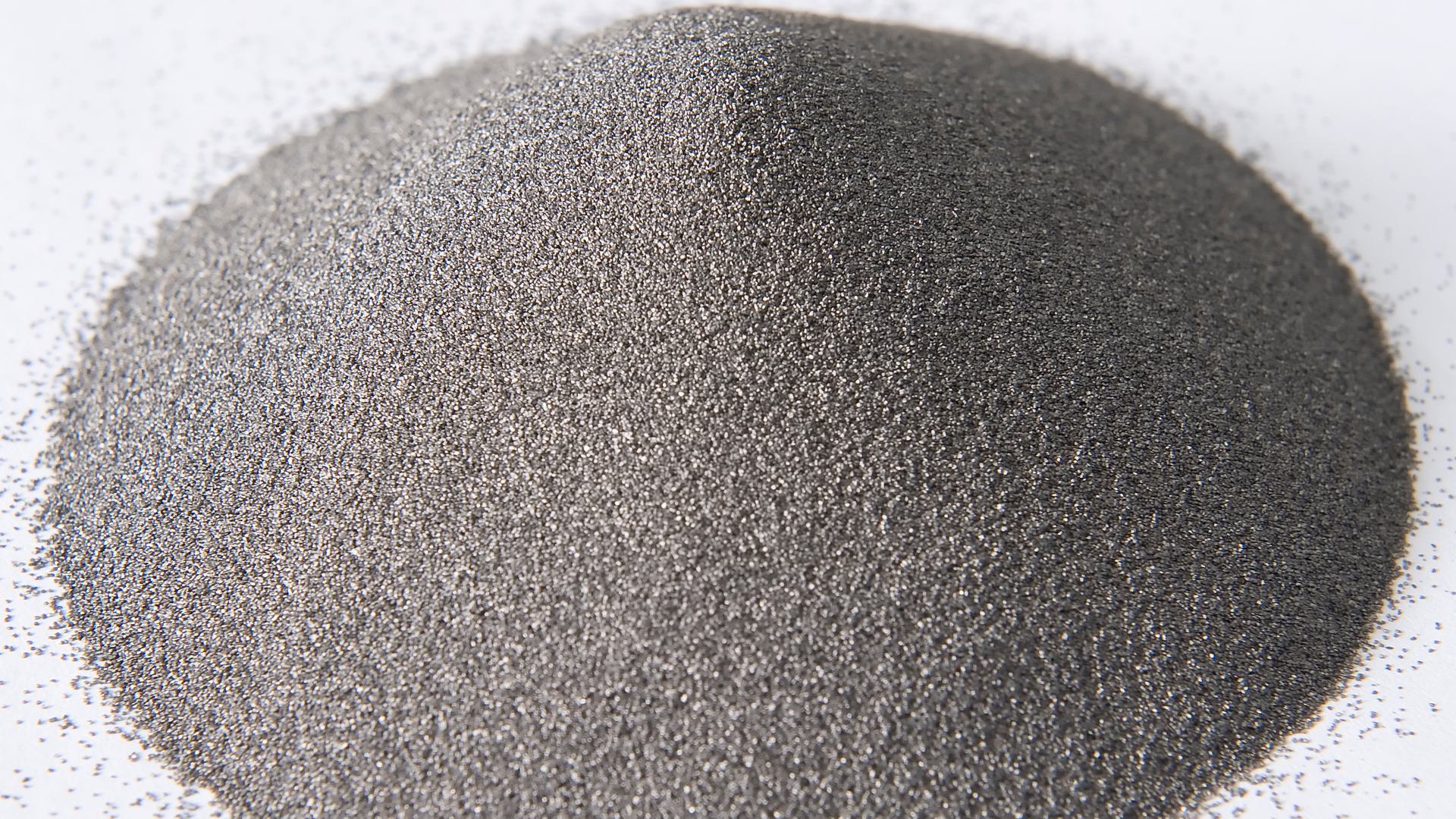
Multiple advantages for the patient
So, what does a prothesis created with Tekna’s Ti64 powder provide for a patient?
By combining Tekna powder characteristics and the dramatically quick pace 3D printing provides when compared to traditional manufacturing methods used to produce medical protheses, patients can receive their implant with less waiting time, thus speeding up their recovery journey.
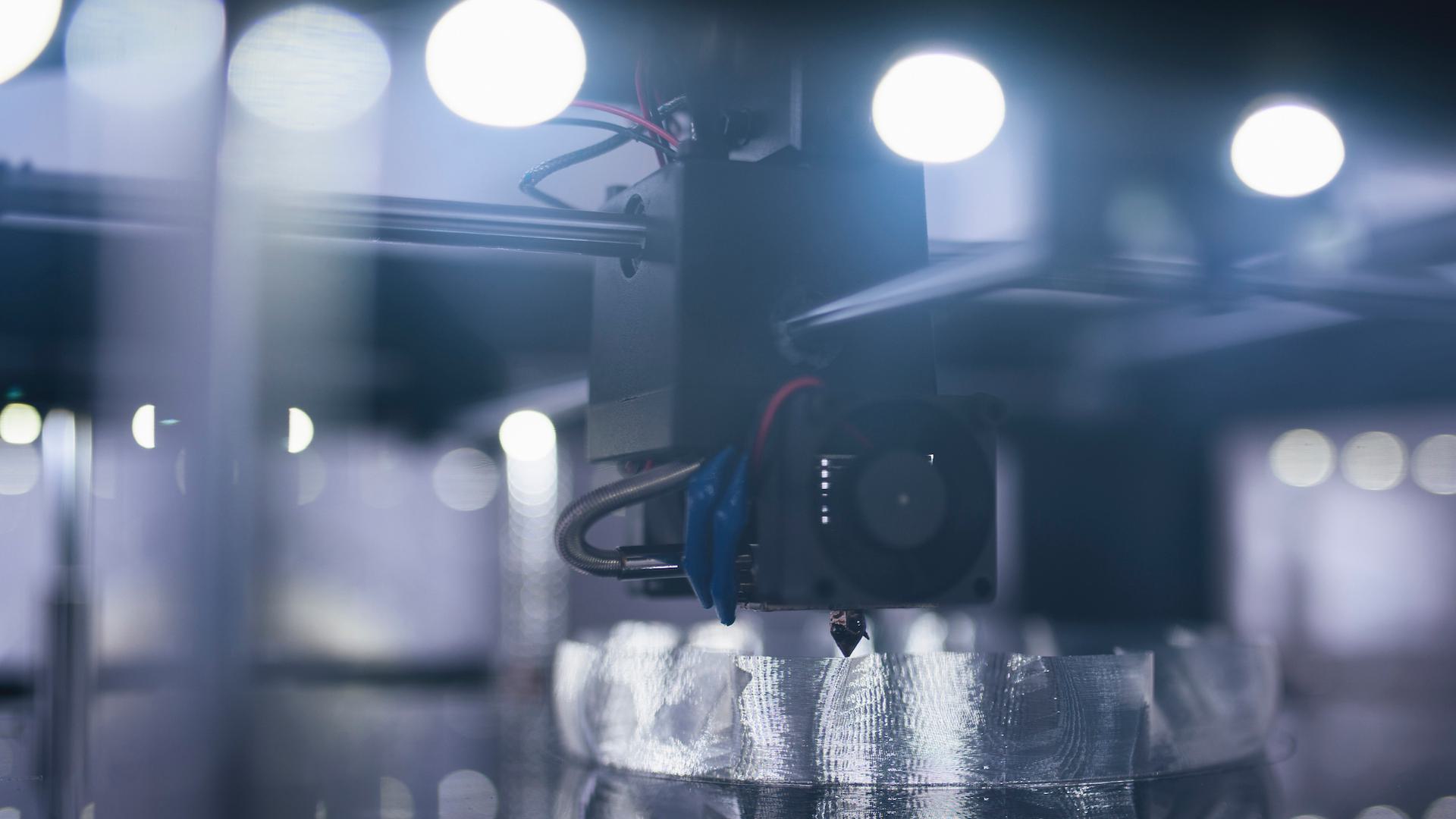
“Currently in the advanced medical field, Ti64 powder is mostly used to 3D print cranial and hip implants,” says Tisserand. “One of the biggest benefits is the improved precision which allows for a more customized prosthesis produced in very short lead times.”
For example: a patient who is in need of a hip replacement. Through traditional methods, the patient would receive a generic implant, which may not perfectly align with their hip joint, potentially leading to pain and instability. With metal 3D printing, the assisting medical team can work with the manufacturers to design a hip implant that precisely matches the patient's hip joint, offering improved mobility, comfort, and overall quality of life.
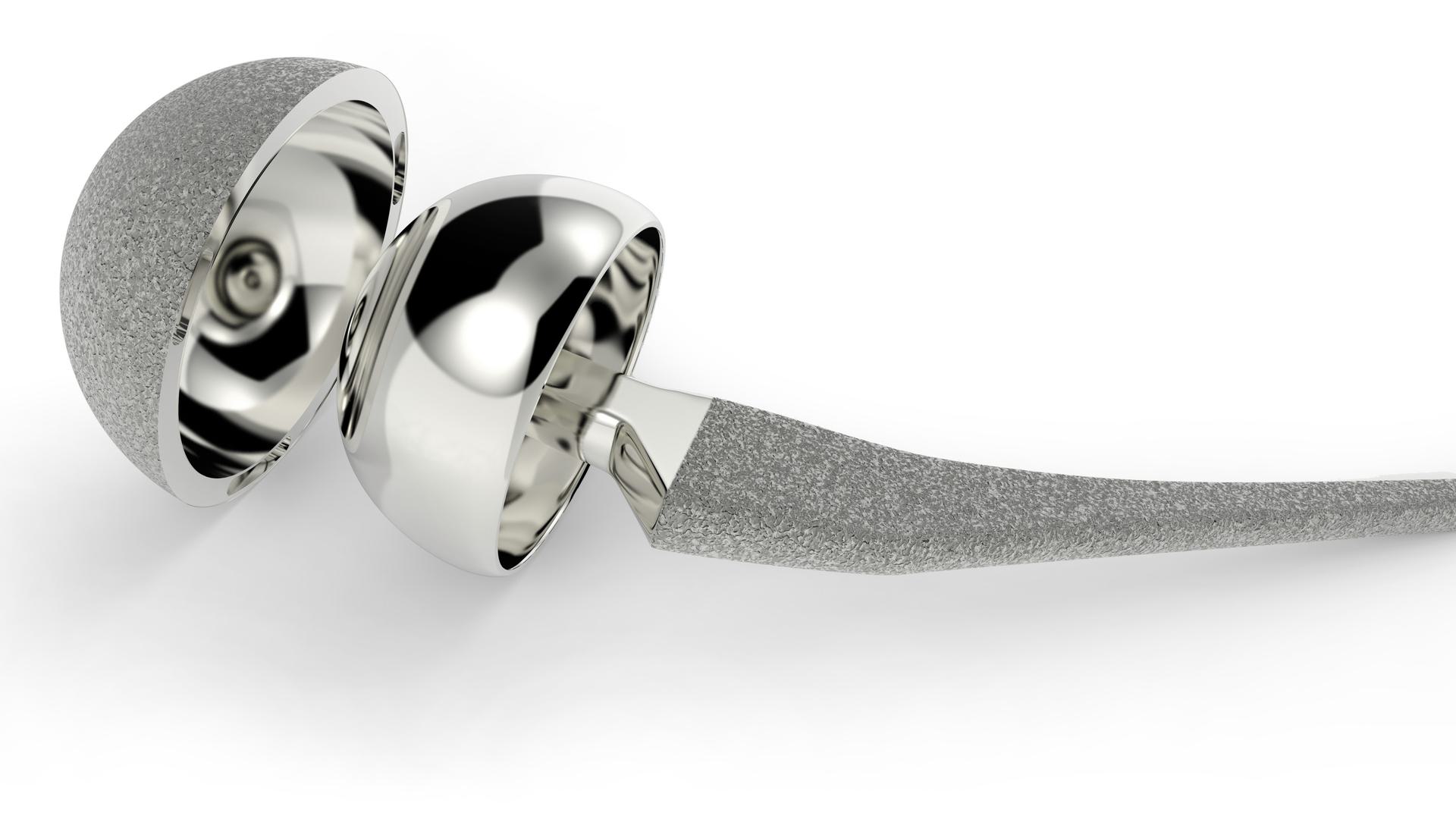
Long-Term Success
Tekna powders are well-established with a growing customer base.
“At the moment, Tekna is experiencing strong sales in North America and Europe. Our customer pipeline is continuously growing which is very promising and exciting,” says Tisserand. “The entire Tekna team is working constantly to meet the most demanding expectations of our customers. We are also engaged in new product developments in collaboration with market leaders to secure our positioning for the future.”
The combination of additive manufacturing technologies and Tekna powders provides significant innovations and improvements in the medical industry. Implants can be manufactured faster with customized designs. Compared to traditional manufacturing technologies, additive manufacturing uses five to ten times less raw material and hence, reduces both carbon footprint and waste. And for Tekna’s 10-year projection:
As the medical market continues to evolve, the company remains committed to pioneering innovations that drive economic, safety, and productivity advancements, setting new benchmarks for quality and performance.
For more information about Tekna powders, look here: https://www.youtube.com/watch?v=QTbvN7k3vg4&t=1s
About TEKNA:
Tekna is a world-leading provider of advanced materials and plasma systems to several industries. Tekna produces high-purity metal powders for applications such as 3D printing in the aerospace, medical and consumer electronics sectors, as well as optimized induction plasma systems for industrial research and production.